The Definition of Supply Chain Risk Management
Supply Chain Risk Management (SCRM) identifies, assesses, controls, and mitigates potential risks throughout a company’s supply chain.
The goal of SCRM is to minimise the impact of supply chain disruptions on the company’s operations, reputation, and bottom line.
Supply chain risks can come from various sources, such as political instability, natural disasters, supplier bankruptcy, transportation disruptions, and attacks that can lead to cybersecurity risks.
SCRM involves proactively identifying these potential risks and developing strategies to minimise their impact, such as diversifying suppliers, building strong relationships with suppliers, establishing contingency plans, and regularly reviewing supply chain processes.
Effective SCRM requires collaboration and communication with all stakeholders in the entire supply chain, including suppliers, manufacturers, distributors, and customers.
By implementing best practices and utilising risk management tools, companies can build a more resilient and sustainable supply chain and minimise the impact of potential disruption.
The Importance of Supply Chain Risk Management in the Business Environment
Today, SCRM is integral to ensuring the success of companies and organisations. With the emergence of new technologies, the globalisation of markets, and the increased complexity of the global supply chain, organisations need to anticipate, manage, and respond to risks associated with their supply chains. SCRM helps organisations mitigate the risks of supply chain disruptions, security threats, and other supply chain-related risks.
SCRM enables organisations to proactively identify and address supply chain issues before they become significant problems. By doing so, supply chain risks can be minimised, allowing organisations to remain competitive and profitable.
The benefits of SCRM are numerous. It allows organisations to identify potential risks and take corrective measures before they become significant issues. It also helps organisations maintain business continuity by reducing supply chain-related costs, improving efficiency, and increasing customer satisfaction.
Furthermore, it can help organisations increase visibility into their supply chains, allowing them to better monitor and manage their suppliers’ performance.
In addition to its many benefits, SCRM helps organisations protect their reputation and brand. By taking proactive steps to mitigate supply chain risks and protect their brand image, organisations can reduce the risk of negative publicity.
SCRM is essential in today’s business environment, as the risks associated with supply chains are increasing. Organisations must proactively identify and mitigate supply chain risks to remain competitive and successful. With the right SCRM strategies, organisations can reduce supply chain costs, improve efficiency, and protect their reputation.
Identifying Supply Chain Risks
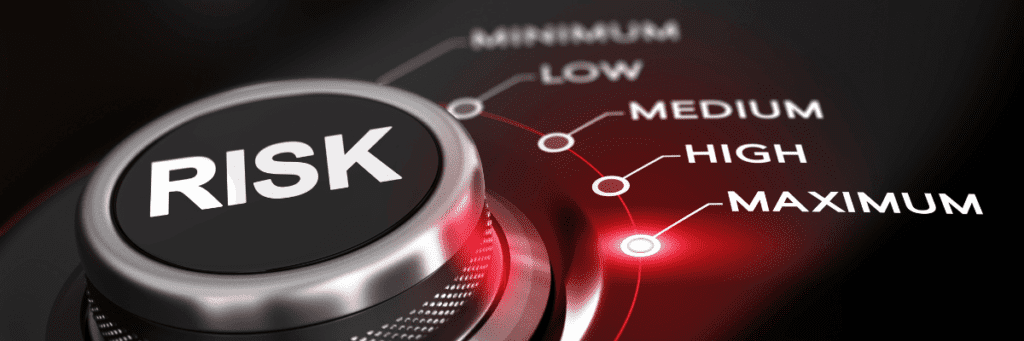
Types of Supply Chain Risks
External Risks
Political Risks
Political risks associated with a supply chain include factors related to political instability or changes in government policies.
These factors can affect the sourcing, production, or distribution of goods and services. Some examples of external political risks in the context of a supply chain include:
- Trade disputes or tariffs can lead to increased costs or disruptions in the flow of goods across borders
- Changes in regulations or trade policies can affect the availability or cost of raw materials, components, or finished products
- Political unrest or conflicts in countries where suppliers or manufacturers are located can lead to disruptions in production or delivery
- Embargoes or sanctions can limit access to specific markets or suppliers
- Changes in environmental or labour regulations can affect the cost or availability of inputs or how products are produced
Businesses need to monitor and manage political risks to ensure the continuity of their supply chain operations. This can involve developing contingency plans, diversifying suppliers, and building solid relationships with government officials and other stakeholders to help navigate potential disruptions.
Economic Risks
Economic risks associated with a supply chain can include various economic conditions affecting the sourcing, production, or delivery of goods and services. Some examples of external threats in the context of a supply chain include:
- Fluctuations in currency exchange rates can affect the cost of inputs or the price of finished products
- Changes in interest rates or inflation can impact the cost of financing or the affordability of products
- Changes in consumer spending patterns or economic growth can affect demand for products and services
- Disruptions in global financial markets or supply chains can affect the availability of credit or the ability to deliver products
- Changes in commodity prices or input costs can impact the cost of production or the availability of inputs
Businesses can manage external economic risks by developing strategies that can help them adapt to changing economic conditions and ensure the company has supply chain resilience. This can involve hedging against currency changes, diversifying suppliers and markets, developing flexible pricing and supply chain structures, and engaging in risk-sharing partnerships with suppliers or other stakeholders. It is essential to regularly monitor and analyse economic trends to identify potential risk threats and opportunities for the supply chain.
Natural Disasters
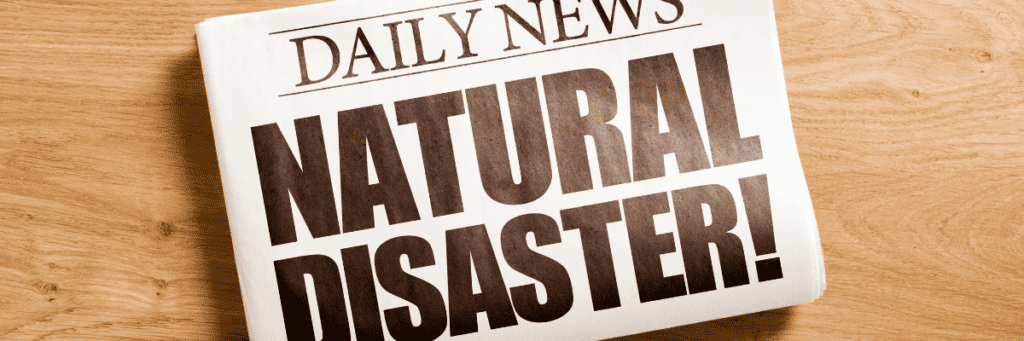
Natural disaster risks associated with a supply chain can include a range of factors related to severe weather events, geological phenomena, and other natural disasters. These can impact the sourcing, production, or delivery of goods and services.
Some examples of natural disaster risks in the context of supplier risk management include:
- Earthquakes, tsunamis, or volcanic eruptions can disrupt transportation infrastructure or damage manufacturing facilities
- Flooding or hurricanes can damage or destroy warehouses, distribution centres, or shipping ports
- Drought or other weather-related events can impact the availability or quality of raw materials or agricultural products
- Forest fires or other environmental disasters can disrupt transportation or damage production facilities
- Pandemics or other health-related crises can affect the availability of labour or the ability to transport goods and services
Businesses can manage natural disaster risks by developing contingency plans that can help them respond quickly to disruptions. This can involve building redundancy into the supply chain, such as diversifying suppliers or distribution centres, investing in alternative transportation modes or routes, and implementing risk-sharing agreements with suppliers or other stakeholders. It is essential to regularly assess the potential impact of natural disasters on the supply chain and to take proactive steps to minimise the impact of potential disruptions.
Internal Risks
Operational Risks
Operational risks associated with a supply chain can include a variety of factors related to the management and operation of the supply chain itself. Some examples of operational risks in the context of a supply chain include the following:
- Quality control issues can lead to product defects or recalls
- Inefficient or unreliable transportation or distribution systems can lead to delays or disruptions in delivery
- Inaccurate demand forecasting or inventory management can lead to overstocking or stockouts
- Inadequate communication or collaboration among supply chain partners can lead to misunderstandings or delays
- Poorly designed or maintained production or processing equipment can lead to breakdowns or other disruptions
Businesses can manage operational risks by:
- Developing robust quality control systems
- Investing in efficient and reliable transportation and distribution systems
- Implementing effective demand forecasting and inventory management practices
- Improving communication and collaboration among supply chain partners
- Investing in the maintenance and upgrading of production or processing equipment
It is essential to regularly monitor and assess operational risks to identify potential issues and implement proactive solutions to minimise the risk of disruptions.
Financial Risks
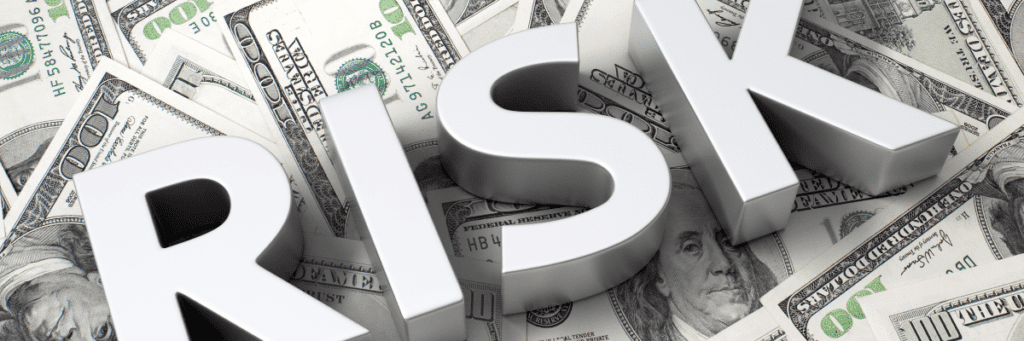
Financial risks associated with a supply chain can include a variety of factors related to the management of financial resources and the financial health of supply chain partners. Some examples of financial risks in the context of a supply chain include:
- Inadequate cash flow management can lead to payment delays or supply chain disruptions
- Poor credit management practices can lead to payment defaults or supply chain disruptions
- Inadequate financial transparency or reporting can make it difficult to assess the financial health of supply chain partners
- Insufficient or poorly designed risk management policies can lead to unexpected financial losses or supply chain disruptions
- Inadequate working capital can make it challenging to finance supply chain operations or investments
Businesses can manage financial risks by:
- Implementing adequate cash flow and credit management practices
- Improving financial transparency and reporting among supply chain partners
- Developing robust risk management policies and procedures
- Investing working capital to support supply chain operations and investments
It is essential to regularly monitor and assess financial risks to identify potential issues and implement proactive solutions to minimise the risk of disruptions.

How to Identify Supply Chain Risks
Conduct a Supply Chain Risk Assessment
Conducting a supply chain risk assessment involves risk identification, risk analysis, and evaluating potential risk exposure that could impact the supply chain’s sourcing, production, or delivery of goods and services. Here are some general steps to conduct a supply chain risk assessment:
- Identify the scope of the supply chain: define the boundaries of the supply chain, including suppliers, manufacturers, distributors, logistics providers, and customers.
- Identify potential sources of risk: review external and internal factors that could impact the supply chain, such as natural disasters, economic conditions, political factors, and operational risks.
- Evaluate the potential impact of each risk: assess the likelihood and potential impact of each risk on the supply chain, such as disruptions in product delivery, increased costs, or reputational damage.
- Prioritise risks: rank them in order of importance based on their potential impact on the supply chain and the likelihood of occurrence.
- Develop risk management strategies: identify and implement risk management strategies that can help control the likelihood and mitigate the impact of potential risks, such as building redundancy into the supply chain, developing contingency plans, or implementing risk-sharing agreements with suppliers or other stakeholders.
- Monitor and reassess: continuously monitor and reassess the supply chain risk landscape to identify new or emerging risks and update risk management strategies as necessary.
It is essential to involve key stakeholders in the supply chain risk assessment process, such as suppliers, logistics providers, and customers, to ensure that all potential sources of risk are identified and addressed.
Additionally, leveraging technology and data analytics can help facilitate the supply chain risk assessment process by providing real-time data and insights to inform risk management strategies.
Gather Data From Various Sources
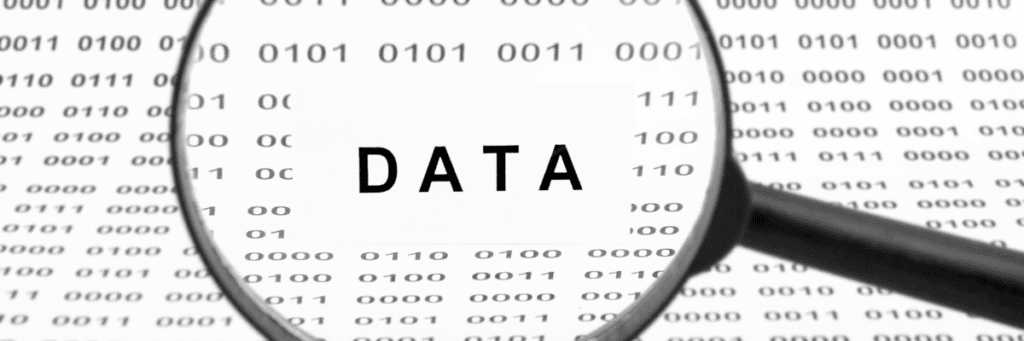
There are a variety of sources of data that can be used for a supply chain risk assessment. Here are some examples:
- Historical data: such as natural disasters, political events, or labour strikes, can be analysed to identify potential risks and inform risk management strategies
- Market data: such as economic indicators, commodity prices, and exchange rates, can be used to assess the potential impact of economic risks on the supply chain
- Weather data: such as forecasts and historical patterns, can be used to assess the potential impact of natural disasters on the supply chain
- Supplier data: such as financial statements, production capacity, and quality performance, can be used to assess the financial health and operational capabilities of suppliers
- Logistics data: such as shipping times, transit times, and lead times, can be used to assess the reliability and efficiency of transportation and distribution systems
- Compliance data: such as regulatory requirements and supplier code of conduct violations, can be used to assess potential legal and reputational risks
- Social media and news data: used to monitor and assess emerging risks, such as political instability or pandemics
It is crucial to select and analyse data sources that are relevant and meaningful to the supply chain under assessment and to leverage technology and data analytics tools to help facilitate the data collection and risk analysis process.
Utilise Supply Chain Risk Management Tools
Various tools can be utilised for supply chain risk management, including software applications such as GetRiskManager, a cloud-based platform designed to help businesses identify, assess, and manage risks.
Other examples of supply chain risk management tools include data analytics tools and simulation models.
These tools can help businesses automate and streamline the supply chain risk management process and provide real-time data and insights to inform risk management strategies. However, it is crucial to carefully evaluate and select the right tool or combination of tools based on the specific needs and characteristics of the assessed supply chain.
Managing Supply Chain Risk
Strategies for Controlling and Mitigating Supply Chain Risks
Diversification of Suppliers
Diversifying suppliers is a common strategy for controlling and mitigating supply chain risks. Here are some techniques that can be used to manage supply chain risks within the diversification of suppliers:
- Conduct supplier assessments of existing and potential suppliers to ensure they meet quality, capacity, and financial requirements
- Establish redundancy: identifying alternate sources of supply, dual sourcing, or using multiple suppliers for the same material or component
- Develop contingency plans that outline how the supply chain will respond to disruptions, such as identifying alternate routes or modes of transportation or pre-qualifying backup suppliers
- Maintain regular contact with suppliers to ensure they meet delivery and quality requirements and quickly identify and resolve issues
- Supply chain visibility: implement tools that provide real-time data and insights into the supply chain to identify potential risks and proactively manage them
- Foster supplier relationships: collaborate on product development, provide incentives for improved performance, and build trust through open and transparent communication
- Diversify geographically: sourcing from suppliers in different regions or countries to reduce the risk of disruption from a single event or region
By implementing these strategies, businesses can better control and mitigate supply chain risks within a diversified supply chain network. It is vital to continuously monitor and reassess the effectiveness of these strategies to ensure that the supply chain remains resilient to potential risks.
Building Strong Relationships with Suppliers
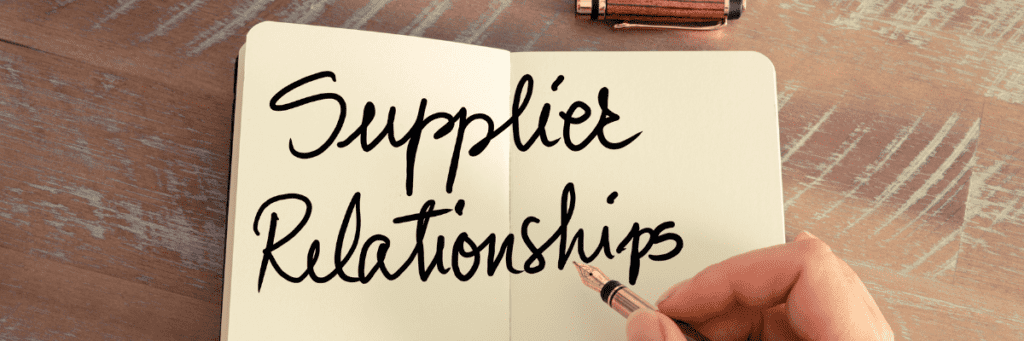
Building solid supplier relationships is critical for any business that relies on a supply chain. Here are some strategies that can be used to build strong relationships with suppliers:
- Communicate openly and frequently to help build trust and promote a better understanding of each other’s needs and goals. This can help to resolve issues more quickly and proactively manage potential risks
- Being reliable and consistent in your dealings with suppliers, such as paying on time and meeting agreed-upon commitments, can help build a positive reputation and foster long-term relationships
- Collaborating on product development with suppliers can help build stronger relationships and lead to more innovative and high-quality products. This can also help to increase efficiency and reduce costs in the supply chain
- Offer incentives for improved performance, such as discounts or longer-term contracts, can encourage suppliers to deliver higher quality products or services and help build loyalty and commitment
- Providing clear expectations and guidelines for supplier performance can help ensure that both parties are aligned and working towards the same goals. This can help reduce misunderstandings and disputes and promote a more effective and efficient supply chain
- Visit suppliers in person: build personal relationships and better understand their operations, capabilities, and challenges. This can help to identify potential risks and opportunities for improvement in the supply chain
By building solid supplier relationships, businesses can benefit from excellent reliability, increased innovation, and a more efficient and effective supply chain. However, continuously monitoring and maintaining these relationships is crucial for long-term success.
Implementing Risk-Sharing Agreements
Risk-sharing agreements are contractual arrangements between businesses and suppliers that outline the sharing of risk and reward in the supply chain. Here are some strategies for creating effective risk-sharing agreements with suppliers:
- Define clear roles and responsibilities of each party in the agreement to ensure that both parties understand their obligations and how risk and reward will be shared
- Align incentives: setting common goals tied to the supply chain’s success. This can help to create a sense of partnership and shared responsibility
- Establish performance metrics: measure the success of the risk-sharing agreement, such as quality, cost, delivery, or innovation. These metrics should be monitored regularly and used to evaluate the success of the agreement
- Allocate risk appropriately: based on the capabilities and resources of each party. This can help minimise potential risk impact on the supply chain
- Use risk-sharing mechanisms: such as insurance, guarantees, or contingency plans to protect against potential risks that are beyond the control of either party
- Foster open communication between parties can quickly identify and resolve possible issues. This can help reduce potential risk impact on the supply chain
- Collaborate on risk management, such as developing contingency plans or sharing information about potential risks to proactively manage risk and increase the resilience of the supply chain
By using these strategies, businesses can create effective risk-sharing agreements with suppliers that promote partnership, align incentives, and help manage potential supply chain risks. It is essential to evaluate and adjust these agreements regularly based on changing circumstances in the supply chain.
Establishing Contingency Plans
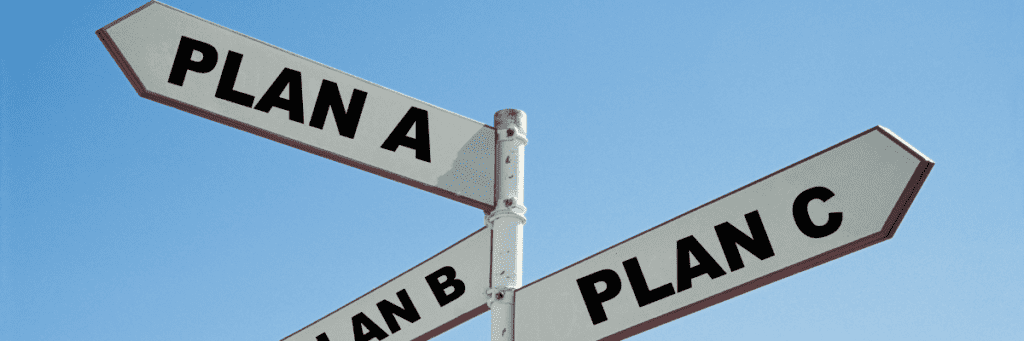
Establishing contingency plans is an essential part of effective supply chain risk management. Here are some strategies for establishing contingency plans for supply chain risks:
- Identify potential risks: conduct a risk assessment by identifying potential threats to the supply chain. This will help you to prioritise and plan for the most significant risks
- Create a risk response team of cross-functional experts responsible for managing risk in the supply chain. This team should have clear roles, responsibilities, and decision-making authority
- Develop response plans for each identified risk, including pre-defined actions, timelines, and communication plans. These plans should be regularly reviewed and updated as circumstances change
- Diversify the supplier base to reduce the risk of disruptions from a single supplier. This can include identifying backup suppliers or alternate sources for critical materials.
- Stockpile inventory of critical materials or finished goods to buffer against potential disruptions. This can be particularly useful for high-risk items or in industries where lead times are long
- Use technology, such as real-time monitoring or predictive analytics, to identify potential disruptions before they occur. This can help to proactively manage risks and reduce the impact on the supply chain
- Develop communication plans for internal and external stakeholders during a disruption. This should include clear lines of communication, escalation procedures, and a method for ongoing communication throughout the disruption
Businesses can use these strategies to establish effective contingency plans for supply chain risks. These plans must be regularly reviewed and tested to ensure they are up-to-date and effective in managing potential disruptions.
Best Practices for Controlling and Mitigating Supply Chain Risks
Regular Review of Supply Chain Processes
Regularly reviewing supply chain processes is essential to effective supply chain management. Here are some steps to take when conducting a review:
- Define the scope of the evaluation, including the specific processes or areas of the supply chain to be reviewed
- Identify Key Performance Indicators (KPIs) relevant to the review’s scope. These KPIs should be used to measure the performance of the supply chain processes
- Collect and analyse data on the supply chain processes using the identified KPIs. This can include data from internal systems, supplier performance reports, or customer feedback
- Identify areas for improvement: based on the data analysis, identify areas for improvement in the supply chain processes. This can include process inefficiencies, quality issues, or risks that need to be mitigated
- Develop an action plan to address the identified areas for improvement. This should include specific actions, timelines, and assigned responsibilities
- Implement the action plan and monitor progress to ensure that improvements are being made
- Continuously monitor the performance of the supply chain processes and adjust the action plan as needed. This should be an ongoing process to ensure the supply chain operates at peak efficiency
By regularly reviewing supply chain processes, businesses can identify areas for improvement and make changes to increase efficiency, reduce costs, and control and mitigate risks. It is important to involve stakeholders from across the organisation in the review process to ensure that all perspectives are considered.
Regular Communication with Suppliers
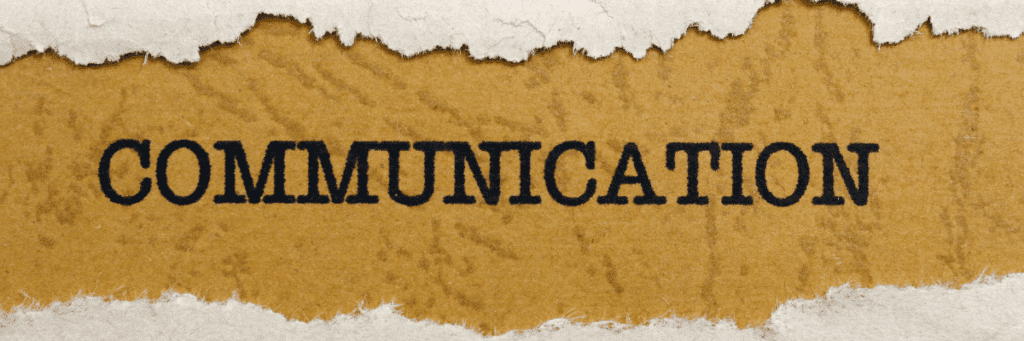
Maintaining regular communication with suppliers is critical for effective supply chain management. Here are some steps to take:
- Set clear communication expectations at the beginning of the relationship, and set expectations for how often and how suppliers should communicate with you. This should include communication channels, response times, and the types of information to be shared
- Use technology to streamline communication with suppliers. This can include tools such as email, messaging apps, video conferencing, and supply chain management software
- Develop a communication plan that outlines the specific topics to be discussed with suppliers and the frequency of communication. This can include regular performance reviews, updates on orders or shipments, and discussions of potential risks or challenges
- Assign clear responsibilities for communication with suppliers to specific individuals or teams. This helps to ensure that communication is consistent and that suppliers have a single point of contact within your organisation
- Prioritise transparency in communication with suppliers. This can include sharing relevant information about your business or industry, providing feedback on supplier performance, and discussing potential risks or challenges
- Provide incentives for suppliers to maintain open communication. This can include performance-based bonuses, preferential treatment for high-performing suppliers, or opportunities for joint problem-solving
By maintaining regular communication with suppliers, businesses strengthen relationships, increase collaboration, and control and mitigate potential risks. Communication must be clear, consistent, and transparent to avoid misunderstandings or disruptions in the supply chain.
Collaboration with Supply Chain Partners
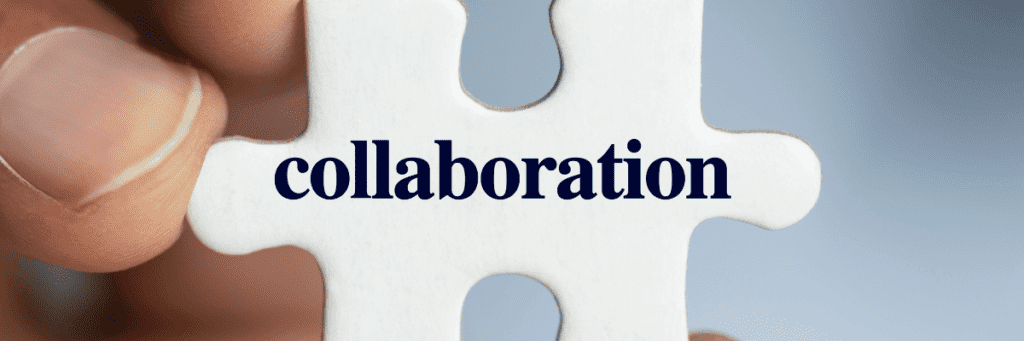
Collaborating with supply chain partners is essential for achieving operational efficiency, reducing costs, and mitigating risks. Here are some steps to take when collaborating with supply chain partners:
- Set common goals and objectives. This helps to align everyone’s efforts towards a common purpose and can improve overall performance
- Foster and build trust and transparency. This can include sharing relevant information, providing feedback, and working together to solve problems
- Share data and information, including demand forecasts, production plans, and inventory levels. This helps to ensure that everyone is on the same page and can respond quickly to changes in demand or supply
- Use technology to facilitate collaboration with your supply chain partners. This can include supply chain management software, data analytics tools, and communication platforms
- Establish clear communication that is consistent, transparent, and responsive. This can include regular meetings, conference calls, and email updates
- Engage in joint problem-solving with your supply chain partners. This can help identify improvement areas, reduce risks, and increase operational efficiency
By collaborating with supply chain partners, businesses can strengthen relationships, increase operational efficiency, and reduce risks. Establishing clear communication channels, fostering trust and transparency, and working together towards common goals are essential.
Managing Supply Chain Disruptions
Managing supply chain disruptions involves minimising the impact of unexpected events on your supply chain. Here are some strategies to consider:
- Identify potential risks that could impact your supply chains, such as natural disasters, economic downturns, and geopolitical events
- Develop contingency plans that outline how you will respond to different supply chain disruptions. This can include backup suppliers, alternative transportation routes, and safety stock
- Monitor your supply chain to detect potential disruptions early. This can include using supply chain management software, conducting regular risk assessments, and maintaining regular communication with suppliers
- Communicate with suppliers regularly to identify potential risks and collaborate on contingency plans. This can help to ensure that everyone is on the same page and can respond quickly to changes in demand or supply
- Implement risk control and mitigation strategies to reduce the impact of disruptions on your supply chain. This can include increasing inventory levels, diversifying suppliers, and using data analytics to forecast demand
- Evaluate your performance in managing supply chain disruptions and identify areas for improvement. This can help you to refine your strategies and ensure that you are better prepared for future disruptions
By proactively managing supply chain disruptions, businesses can reduce the impact of unexpected events on their operations and maintain supply continuity. To this end, it is essential to identify potential risks, develop contingency plans, monitor the supply chain, and collaborate with suppliers.
Strategies for Managing Supply Chain Disruptions
Having an Emergency Response Plan in Place
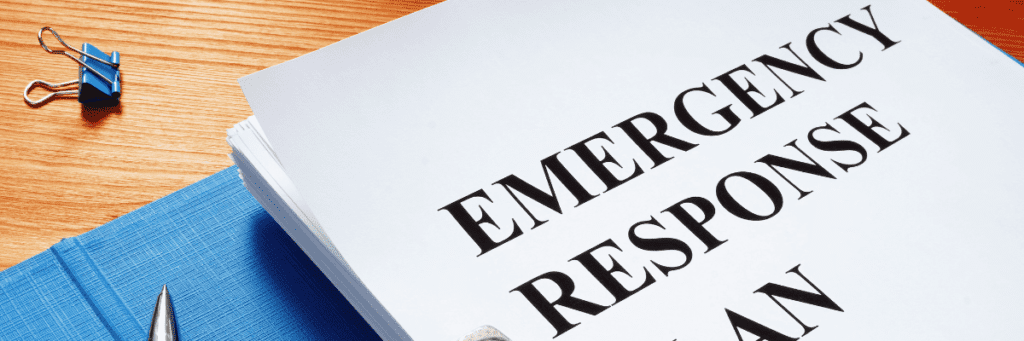
An emergency response plan for managing supply chain disruptions is a detailed plan that outlines the actions to be taken during unexpected events that disrupt the supply chain. The plan should be designed to minimise the impact of disruptions and restore normal operations as quickly as possible. Here are some critical elements of an emergency response plan:
- Risk assessment: conduct a risk assessment to identify potential risks impacting your supply chain. This can include natural disasters, economic downturns, geopolitical events, and other factors
- Emergency response team: establish an emergency response team responsible for managing the response to supply chain disruptions. This team should include key stakeholders from different areas of the organisation
- Communication plan: develop a communication plan that outlines how the information will be shared with stakeholders during a supply chain disruption. This plan should include both internal and external communication channels
- Contingency plans: develop contingency plans that outline how you will respond to different supply chain disruptions. This can include backup suppliers, alternative transportation routes, and safety stock
- Recovery plan: develop a recovery plan outlining restoring normal operations after a disruption. This plan should include steps for assessing damage, restoring systems, and resuming operations
- Testing and training: test and train your emergency response plan to ensure that it is effective and that key stakeholders know what to do during a disruption. This can include conducting tabletop exercises and simulations
With a well-designed emergency response plan, businesses can minimise the impact of supply chain disruptions and restore normal operations as quickly as possible. To ensure the plan’s effectiveness, conducting a risk assessment, establishing an emergency response team, developing communication and contingency plans, and testing it is essential.
Rapidly Identifying and Addressing the Disruption
Rapidly identifying and addressing supply chain disruptions is crucial to minimise the impact of disruptions on your business. Here are some strategies to consider:
- Establish early warning systems that detect potential supply chain disruptions early. This can include monitoring news and social media, tracking supplier performance metrics, and using supply chain management software
- Regularly communicate with suppliers to identify potential risks and collaborate on contingency plans. This can help you detect disruptions early and respond quickly
- Develop contingency plans that outline how you will respond to different supply chain disruptions. This can include backup suppliers, alternative transportation routes, and safety stock
- Implement risk management strategies to reduce the impact of disruptions on your supply chain. This can include increasing inventory levels, diversifying suppliers, and using data analytics to forecast demand
- Monitor your supply chain to detect potential disruptions early. This can include using supply chain management software, conducting regular risk assessments, and maintaining regular communication with suppliers
- Establish an emergency response team responsible for managing the response to supply chain disruptions. This team should be trained to respond quickly to unexpected events
- Evaluate your performance in responding to supply chain disruptions and identify areas for improvement. This can help you to refine your strategies and ensure that you are better prepared for future disruptions
Businesses can detect potential disruptions and respond quickly by proactively managing supply chain disruptions and establishing early warning systems. Maintaining regular communication with suppliers, developing contingency plans, implementing risk mitigation strategies, monitoring the supply chain, establishing an emergency response team, and evaluating performance to ensure better preparation for future disruptions is vital.
Communicating with All Stakeholders
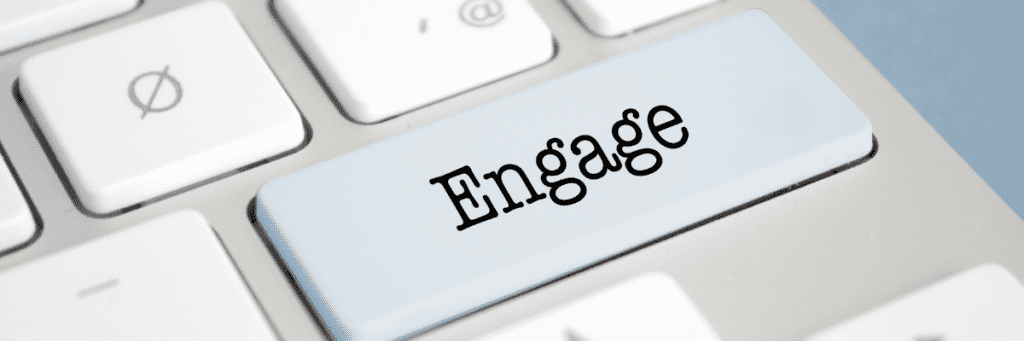
When a supply chain disruption occurs, it is vital to communicate with all stakeholders to keep them informed and to manage expectations. Here are some strategies to consider:
- Establish a communication plan and outline how to communicate with stakeholders during a supply chain disruption. This plan should include who will be responsible for communicating with stakeholders, what information will be transmitted, and how often
- Prioritise communication with key stakeholders, such as customers and suppliers, and ensure they know the disruption and its impact on your business. Be transparent and provide regular updates as the situation evolves
- Use multiple channels, including email, phone, and social media. This will help to ensure that your message reaches a broad audience
- Guide stakeholders in managing the disruption and determining what actions they should take. This can include information on alternative suppliers, changes to delivery schedules, and how to manage inventory levels
- Communicating with stakeholders proactively and anticipating their needs helps reduce confusion and mitigates the impact of disruption on your business
- Follow up after the disruption has been resolved, ensure they are satisfied with the outcome, and identify areas for improvement
Effective communication with stakeholders is essential for managing the impact of supply chain disruptions. By establishing a communication plan, prioritising communication with key stakeholders, using multiple channels, providing guidance, being proactive, and following up, businesses can help minimise disruptions’ impact on their operations and maintain positive relationships with stakeholders.
Implementing Contingency Plans
Implementing a contingency plan during a supply chain disruption involves several steps:
- Identify the disruption: the first step is to identify the supply chain disruption and assess its impact on your operations. This will help you determine the disruption’s extent and the resources required to implement the contingency plan.
- Activate the contingency plan: once the disruption has been identified, activate the contingency plan. This may involve implementing alternative sourcing strategies, changing delivery schedules, or modifying production processes.
- Communicate the contingency plan to all stakeholders, including suppliers, customers, and employees. This will help manage expectations and ensure everyone knows how to address the disruption.
- Monitor the progress of the contingency plan and adjust as required. This may involve changing sourcing strategies, adjusting inventory levels, or modifying production processes.
- Evaluate the effectiveness of the contingency plan: after the disruption has been resolved, evaluate the effectiveness of the contingency plan. This will help identify improvement areas and ensure the business is better prepared for the future.
Implementing a contingency plan during a supply chain disruption requires careful planning, effective communication, and ongoing monitoring. By following these steps, businesses can help mitigate the impact of disruptions on their operations and maintain the trust and confidence of their stakeholders.
Final Thoughts
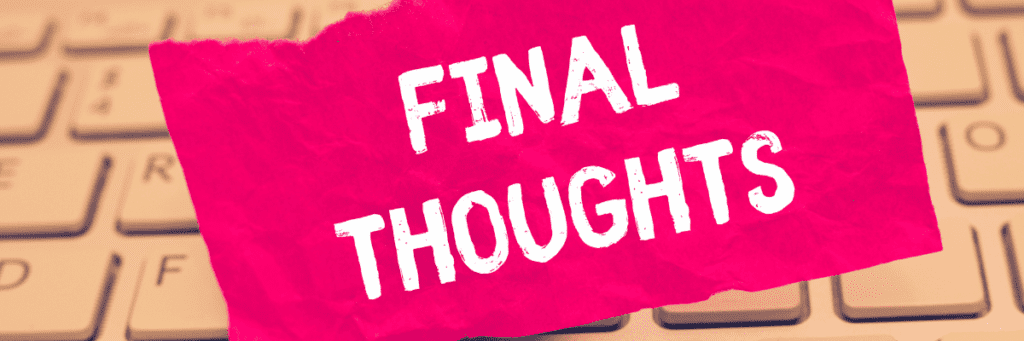
Supply chain risks can come from various external and internal sources, including natural disasters, economic and political factors, operational issues, and financial risks.
Conducting a supply chain risk assessment involves identifying potential risks, evaluating their likelihood and impact, and developing strategies to manage and mitigate them.
Strategies for controlling and mitigating supply chain risks include diversifying suppliers, building strong relationships with suppliers, establishing risk-sharing agreements, and establishing contingency plans.
Maintain regular communication with suppliers and collaborate with supply chain partners. Businesses should establish clear communication channels, provide timely updates, and maintain open lines of communication.
In managing supply chain disruptions, businesses should have an emergency response plan, rapidly identify and address disruptions, communicate with all stakeholders, implement a contingency plan, and regularly review and evaluate their processes.
Communication with stakeholders during a supply chain disruption is essential. Businesses should prioritise communication with key stakeholders, use multiple channels, provide guidance, be proactive, and follow up to ensure stakeholders are satisfied with the outcome.